Good Manufacturing Practices (GMP)
What is GMP?
Good Manufacturing Practices (GMP) is a system that ensures manufacturing products such as food, cosmetics, and pharmaceutical goods which are consistently produced and controlled according to set quality standards. GMPs examine and cover every aspect of the manufacturing process to guard against any risks that can be catastrophic for products, such as cross-contamination, adulteration, and mislabeling. Implementing GMP can help cut down on losses and waste, and protects both the company and consumer from negative food safety events.
What are GMP Guidelines?
GMP guidelines are a set of principles that help manufacturers implement an effective manufacturing process and ensure that quality is built into the organization and the processes involved. GMP guidelines are customarily flexible, with countries having their own legislation to comply with local GMP guidelines and principles. But almost all regulations are derived from the basic concept and guidelines which are explained as Good Manufacturing Practices (GMP) .
12 G's of GMP
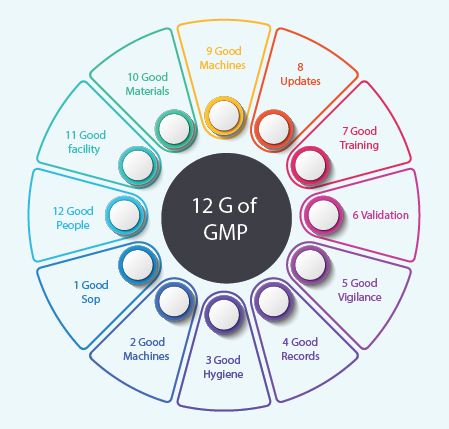
1. Good SOP:
Standard Operating Procedures are issued to instruct employees in areas of responsibility, work instructions, appropriate specifications and required records. A Good SOPs are the documents which helps the employees to work efficiently on the task which were allocated to them with having minimal errors.
2. Good Methods:
Good methods are very useful for the manufacturers where they can use them at the time of manufacturing the product without any defects are faults. Basically, in pharmaceuticals, methods are nothing but tests which are used to test the product at the time of manufacturing.
3. Good Hygiene:
Your personal hygiene is very important. All personnel working in the production area are expected to maintain a high degree of personal cleanliness. The following things that a manufacturer has to make sure that are Personal hygiene, cleanliness, handling of the products, illness and injuries, Cross-contamination etc.
4. Good Records:
These records are the only real source of information on a batch after it has been released or the time of production for inspection purpose too, so they must be accurate and complete. They provide legal evidence that the company followed GMP.
5. Good Vigilance:
Keeping an eye on the each and every operation done by the employee or the results of the operation makes us to eliminate the errors of the products mostly. All these operational vigilance can be done by the superiors, in the form of approvals.
6. Validation:
Validation is the analysis of data gathered throughout the design and manufacturing of a product in order to confirm that the process can reliably output products of a determined standard. It may be either Vendor Validation or Performance Validation etc.
7. Good Training:
Effective training programs always impart responsibility in all employees to perform their tasks with utmost care and commitment. In the healthcare manufacturing industry each employee needs job specific training in technical skills, SOPs, and awareness of the GMP. To satisfy this requirement, companies must adopt a systematic approach to training design, development, and implementation. Training helps the pharmaceutical industry to meet the compliance, consumer safety, product quality and to their development.
8. Updates:
As in the part of vigilance, each operation can be given as update to the superiors, which helps us to eliminate the errors at the very first stage itself. Those should be done by getting time to time alerts in the form of emails, or dash board alerts are sending for approvals will do.
9. Good Machines:
The quality of the manufactured product depends on the suitability, and level of the technology of the equipment used. Since, it is major requirement in the manufacture of the pharmaceutical products. The Efficiency of the equipment can be maintained by giving time to time services, calibrations and doing performance validations of the equipments.
10. Good Materials:
All the materials which are used in the pharmaceutical industries should pass the QA. On second hand all the materials should be monitored time to time to avoid using of the expired materials at the time of production and also maintain a good stock, which avoids the situations of running out of stocks which delays the production.
11. Good Facility:
To provide a good manufactured product, the facility also plays a prominent role. As the organization should built the facility which is suitable for the production like, labs, culturing rooms, equipment rooms and also should maintain the premises clean and tide, which avoid cross-contaminations etc.
12. Good People:
The GMPs for a manufacturing facility must be strictly adhered to and this cannot be done without proper GMP training for personnel. All people involved in making a drug must have clear roles and responsibilities. Employees must know how to follow procedure and their performances must be assessed. This also means that the training methods must be reviewed, so that manufacturer knows how it can ensure their employees are properly trained and competent.
CodonLIMS has all the above mentioned 12 G's of GMP seamlessly and maintains the data for GMP compliant facilities.